In the last months, SINTEF developed a lubrication free turbo-compressor for the steam heat pump of the FRIENDSHIP system.
The designed compressor prototype allows temperature lifts of up to 30 Kelvin in a single stage compression and was dimensioned to a capacity range of around one ton per hour of compressed steam, based on a heat source temperature of 100°C (atmospheric pressure).
The prototype was designed for a multistage compression approach and the last stage has the ambition to achieve a pressure of 15 bar, which will give a condensation temperature of approximately 200 °C.
In October the turbo compressor rig was finally installed in Norway, with a two-stage setup using turbo compressors from Rotrex. The impellers are made from titanium, rotate up to 90.000 rpm and operate oil free. Also, they are equipped with a purge chamber, where pressurized air is used to drain out steam condensate, for improving sealing between the impeller and the oil filled gearbox.
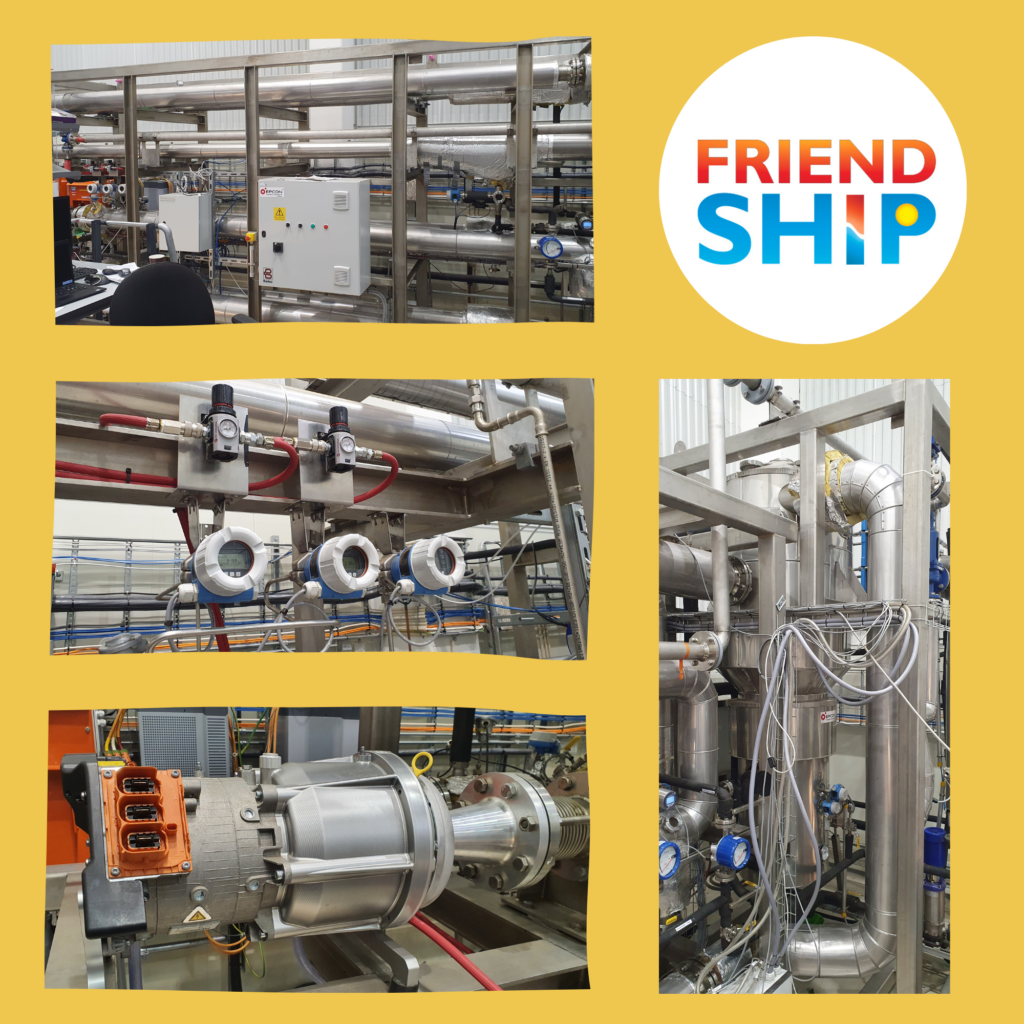
Moreover, after each compression stage de-superheating stage through water injection is employed to reduce the inlet temperature into the next compression stage.
In the end the steam is extended in an expansion valve and regenerated in a condenser, i.e., steam supply tank.
Now it is time to begin the testing phase, which will include the testing of the new compressor flange seals, of the new thermos-seals between compressor section and steam regenerator tank, the testing of water supply and purge air system.